To sort out the twisting of the inner brackets, I now fitted tensioning
bars made out of 8BA threaded brass rod. It turned out that I had
to pull one side in and push the other side out the make it square
again. Once again, it slid freely along the rods.
In order to make the inner brackets move along the threaded rod, I
needed to fit some captive nuts. For the same reason as the Y
axis, two were needed to avoid any backlash. I made two brackets
out of aluminium and trapped the nuts between them and the wooden
bracket.
Here's the combined result:
Moment of truth time. I lashed my miniature drill to the
frontplate and attached the second Stylus Color motor to the threaded
rod which hadn't been cut to the right length yet:
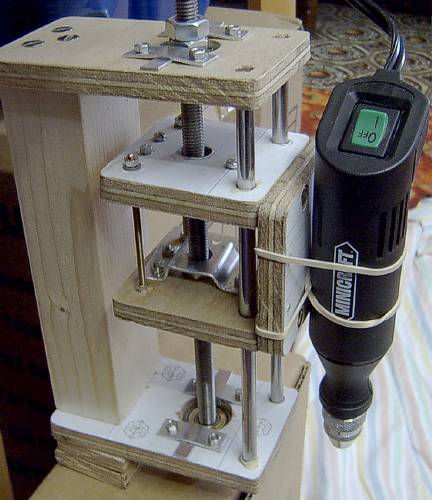
Yes, it had no problem raising and lowering the
mechanism. It was even slower than the Y axis though due to the
higher resolution of the motor.
Now I replaced the regular nuts with lock-nuts, cut the threaded rod to
the right length, fitted aluminium straps to the front plate for the
drill mounting and made a bracket to hold the stepper motor above the
threaded rod. As before, I coupled the motor to the shaft with
hosepipe.
So here is the finished Z axis:
Phew! Well let's press on with the final axis...